If you want to avoid failures, there are two strategies to prevent them. One is preventive maintenance, and the other is predictive maintenance. However, apart from their proactive approach, there are fundamental differences between them. Read on to find out what these differences are.
First of all, what is preventive maintenance?
Preventive maintenance (alternatively, preventative maintenance) measures are planned and performed on equipment to ensure that failures do not occur and to mitigate the consequences of breakdowns. These routine tasks are completed regardless of the current operating condition, i.e. whether it is working well or not.
Preventive maintenance measures are usually determined by time (e.g. every 6 months), usage (e.g. every 500 uses) or milestones (e.g. every 3,000 miles), with parameters that are based on statistics gathered on the expected or average life of the equipment. Because preventive maintenance is time-based or usage-based, you can plan for it in advance. Follow our step-by-step guide to developing a preventive maintenance plan.
⚙️ If you’re looking for a quick fix, you can also download our preventive maintenance plan template in Excel.
Advantages and disadvantages of preventive maintenance
This type of maintenance has many advantages compared to reactive maintenance, which only occurs after equipment failures or breakdowns are reported. Preventive maintenance decreases downtime, increases reliability, and improves safety. According to the US Department of Energy, it yields cost savings of 12-18% compared to reactive maintenance.
The one problem with preventive maintenance is that reports are not based on the actual condition of the equipment. This can lead to unnecessary maintenance, which can waste time and money.
- As much as 50% of maintenance costs are a “waste”, according to IBM
- Around 30% of preventive maintenance is too frequent
- As little as 18% of age-related failures follow a pattern
What is predictive maintenance?
Unlike preventive maintenance, predictive maintenance is based on the current operating condition of an asset rather than on statistics and previously defined schedules. The same report by the US Department of Energy suggests it yields cost savings of about 25-30% compared to reactive maintenance.
The general idea is to use condition monitoring to predict the occurrence of a failure before it ever even happens, which means:
✓ less unplanned downtime
✓ less unnecessary maintenance
✓ fewer costs in MRO materials/inventory;
✓ increased asset lifetime
✓ thorough asset monitoring, which means a shorter mean time to repair, and also the ability to verify the efficacy of maintenance work.
Types of predictive maintenance
Predictive maintenance consists of two steps. The first is condition monitoring, which includes different types of predictive maintenance techniques, including vibration and oil analysis, to assess the equipment’s current state. Quite often, it’s possible to detect early signs of failure before operators notice them – up to 60 to 90 days in advance, according to IBM.
As soon as unwanted conditions such as general wear or misalignment are detected, a repair is scheduled before any actual failure occurs. You can continue to monitor asset condition to make sure maintenance was effective.
💡 Predictive Maintenance Tools (condition monitoring techniques)
- vibration analysis
- acoustic analysis
- infrared analysis
- motor circuit analysis
- thermography
- ultrasonic monitor
- radiography
- laser interferometry
- electric and electromagnetic measurements
Although condition monitoring and predictive maintenance are sometimes used interchangeably, these tools alone do not amount to “predictive maintenance”. Predictive maintenance implies further data analysis. Predictive maintenance algorithms model condition monitoring data to predict when a failure will occur, which is what allows you to take appropriate action.
- You may through root-cause analysis, namely FMEA;
- Integrate the data sets to interpolate and extrapolate;
- Search data about similar assets.
Disadvantages of predictive maintenance vs preventive maintenance
The implementation of a predictive maintenance strategy is usually more costly than a preventive one, as there is a need to invest in predictive maintenance tools, compatible software, and to train staff to use it and to interpret the data collected.
So which strategy should you use: preventive or predictive maintenance?
The best strategy is to have a maintenance program incorporating both of these types of maintenance according to each scenario. Remember that considering reactive maintenance is still (albeit less) necessary when adopting these strategies.
Go on a case-by-case basis and choose the right maintenance strategy for each asset.
Preventive Maintenance | Predictive Maintenance |
You may start preventive maintenance at any time | First, you need to collect data |
Is time and usage-based, in cycles | Identifies potential failures |
Planned in advance | Planned “as you go” |
Low to medium costs, requires maintenance software and preventive maintenance checklists | Medium to high costs, requires condition monitoring software, sensors and tools, plus training |
Usually requires planned downtime for inspections and routine checks | May be performed while machines are running |
Companies need to prepare spare parts and organise inventory | Buy the parts you need and don’t replace parts that still work |
Some work may be done on assets that don’t need it, just for “prevention” | Avoids run-to-failure and unnecessary maintenance |
↪️ Adequate for assets that are hard to monitor, and the cost of failure is high | ↪️ Adequate for assets that are easy to monitor and whose failures are predictable |
↪️ If the cost of analytics is too high, you may use either preventive maintenance or condition monitoring techniques, without the extra predictive analysis. |
Throughout this article, we’ve seen that both preventive and predictive maintenance are proactive, planned, and linked to higher availability and reliability. Another thing they have in common? You’re better off planning them with the right tool.
Intelligent Maintenance Management Platforms, such as Infraspeak, exist precisely to help you define, plan, perform and monitor your maintenance strategy. Schedule a meeting and see for yourself!
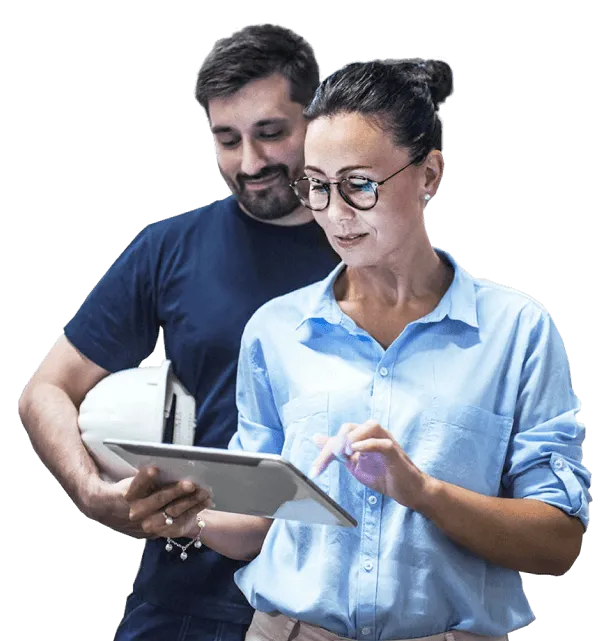